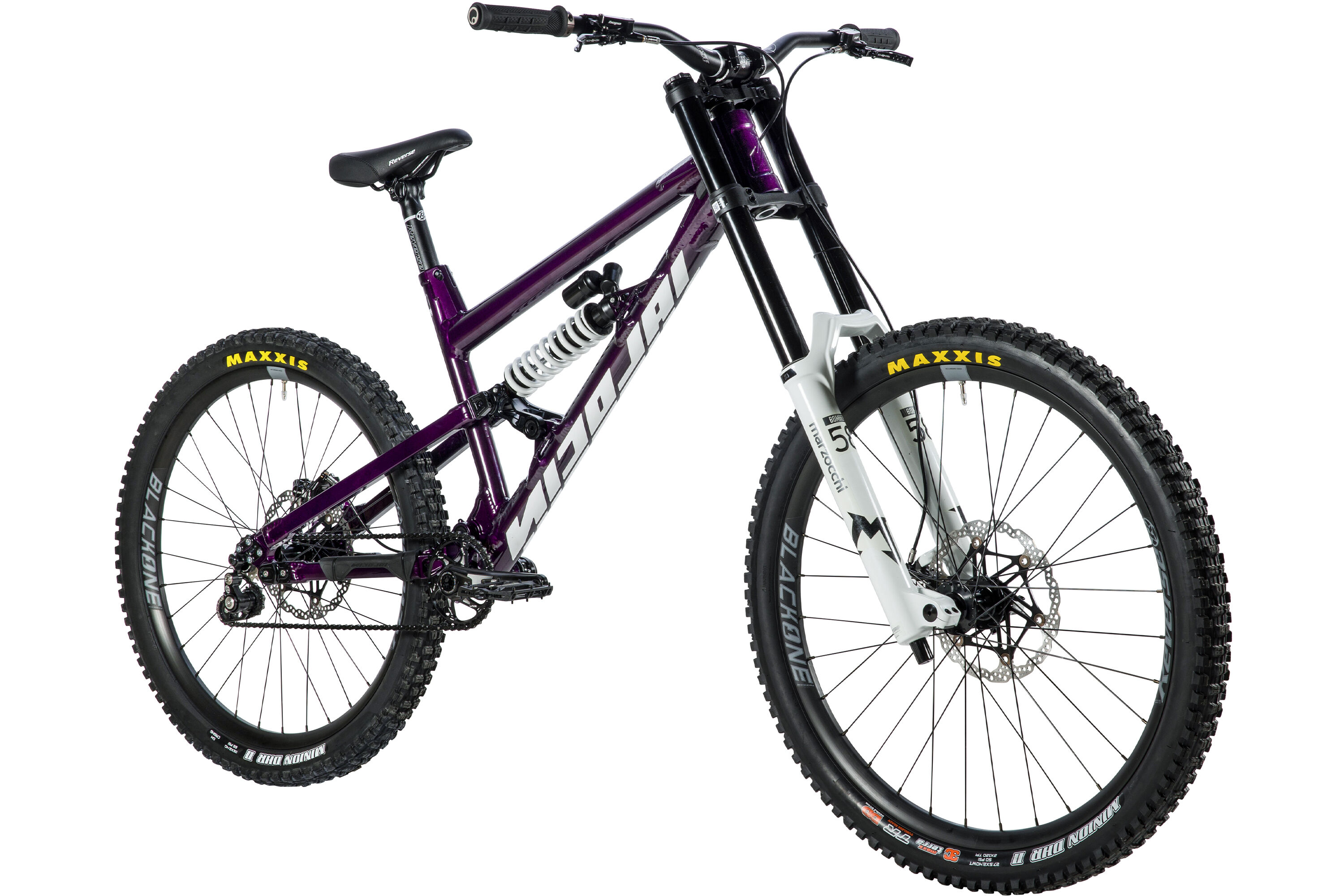

NAIL IT!
Just as radical as the Fest Series and Rampage, the G18 Hammer is a tool for big air, big style and big impacts. We worked closely with our team rider Max Kruse to develop this uncompromising freeride bike. Max is one of the few German pro freeriders and for many years he feels right at home out on the sick jumplines of international freeride events. Max and his crew from the Nicolai Freeride Squad need two things above all for their job that the modified downhill race bikes that are normally used in freeride can't provide: a playful, agile handling and extreme durability.
Topology optimization
Computer-aided design to optimize durability, function and weight
When designing turned and milled parts, we use FEM software (Finite Element Method), which allows us to simulate the loads that will occur in later use in order to determine the optimum shape (topology) of these components. Critical structural areas become visible this way and can be strengthened by adding material, whereas material can be saved at less stressed areas. This way we can produce highly complex parts and assemblies for our frames that combine maximum durability with minimum weight.
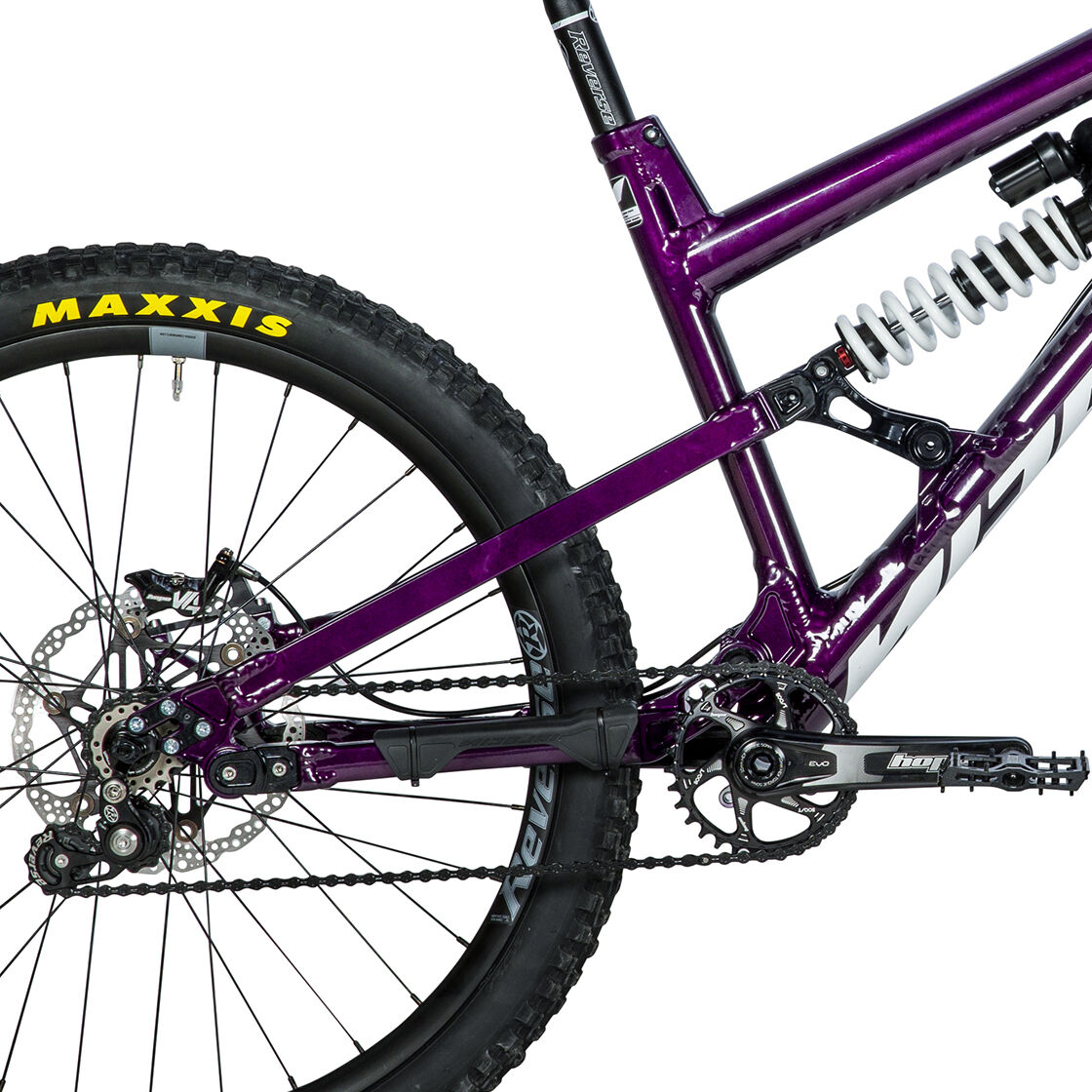
Horst Link
Drive-optimized and brake-neutral four-bar rear end
With our suspension systems, we aim to combine competitive performance and maximum fun on the trail with high pedaling efficiency by kinematically decoupling the rider's movements from the chassis dynamics. For this reason, we design our 4-bar rear ends according to the proven, classic Horst Link principle. The Horst Link is the joint located at the end of the chainstay in front of the rear axle. It counteracts the shortening of the wheelbase during rear compression. Through years of experience and with the help of simulation software, we have succeeded in continually optimizing and refining the Horst Link technology for our bikes. In particular, the anti-squat characteristics of the suspension have been significantly improved.
Insert Bearings
four-fold sealed full-ball groove and angular contact ball bearings
The rear end of a full-suspension bike is subjected to high dynamic loads during riding. The focus here is on the bearing points where the forces are transmitted between the components. The full-ball, double-sealed bearings installed on our frames are made by the ENDURO brand. They not only have top marks for power transmission, but also a particularly low breakaway torque, which ensures sensitive, smooth suspension response. At the same time, they offer the best possible sealing against dirt and moisture for a long service life and long maintenance intervals.
Shocks
Shock technology with individually optimized setups
In order to achieve the maximum potential of a suspension system, the choice of the right rear shock is of decisive importance. We offer two high-performance coil shocks for the G18 Hammer that perfectly match its freeride focus and unlock the full potential of its suspension: the Marzocchi Bomber CR and the Fox Factory DHX2, each with the dimensions 250 x 75 mm. But regardless of whether you choose the reasonably priced Marzocchi Bomber with adjustable compression and rebound damping or prefer the wide tuning spectrum of the Fox Factory: we have tested both shocks with the G18 Hammer and they both come with individual shim stacks ( components in the shock that regulate oil flow and resistance) that are perfectly tuned to the requirements and kinematics of the G18.
Rado
Rear Aligning Dropout
Our RADO dropouts guarantee perfect alignment between the front and rear wheels of the bike. Finalising the toe and camber of the rear wheel and fixing the RADO in an exact position means that every NICOLAI is always one hundred percent straight. Despite precise preparatory work, construction methods and the utmost care, any aluminum frame is subject to a certain amount of heat distortion during the welding process. Of course, after welding, each frame is straightened, precisely measured and the final alignment ensured. Instead of forcing the frame into alignment, the RADO can be precisely fixed in place with guided grooves and the choice of 5 different camber heights. After locating the correct toe position along the guided grooves, the frame is drilled and the RADO is pinned by a dowel. The chosen RADO for each frame has the correct camber dimension milled into the RADO. This means that the original alignment is retained when the dropout needs replacing.
DC Bumper
Fork end stops integrated in head tube gusset
DC Bumpers protect the frame and the upper fork stanchions from damage that may occur when the fork is fully turned in or the handlebars over rotates in the event of a crash. Our DC Bumpers are designed to replace the fork manufacturer's standard end stops. Not only are those usually less attractive and detract from the appearance of the fork, they also reduce the fork clearance and complicate the removal of the stanchion unit from the crown. Another disadvantage is that the original end stops can slip, resulting in damage to the frame and fork. Our Nicolai DC Bumpers are bombproof mounted to the head tube gussets. They provide excellent protection against impacts, allow for quick fork removal and service access, ensure the maximum clearance and on top of that - look really good.
UDH Standard (optional)
Mounting standard for SRAM T-Type rear derailleurs at the thru axle mount
At the UDH standard, a SRAM AXS Transmission rear derailleur is attached directly to the thru axle of the frame rear. These rear derailleurs are designed significantly more stable than regular derailleurs and thus better protected against bending and ripping off. Their higher torsional stiffness also ensures higher shifting precision. SRAM AXS Transmission rear derailleurs are operated electronically and wireless and are optimized for shifting under maximum load. To minimize the effect of significant chain elongation that occurs with a high-pivot design, the Nucleon 16 UDH uses a lower guide pulley on the front chainring in addition to the upper idler. Thus, the returning chain is guided towards the swingarm pivot point, which reduces the elongation during compression. At the same time, this reduces chain slap and effectively prevents the chain from running off. Through the use of the lower guide pulley, the travel of the chain tensioner is within the technical limits that SRAM specifies for its Transmission derailleurs, even when the rear is fully compressed and in any gear.
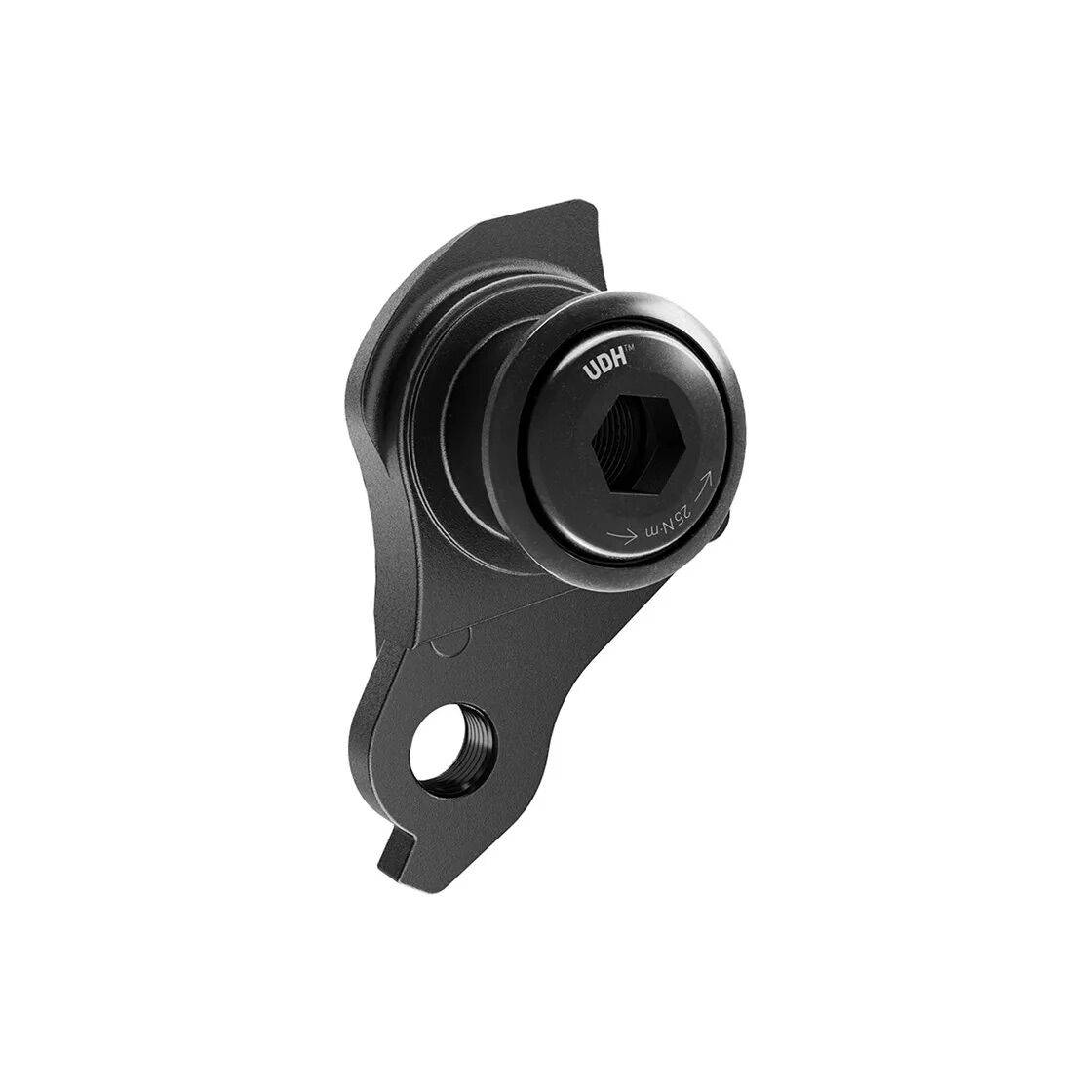
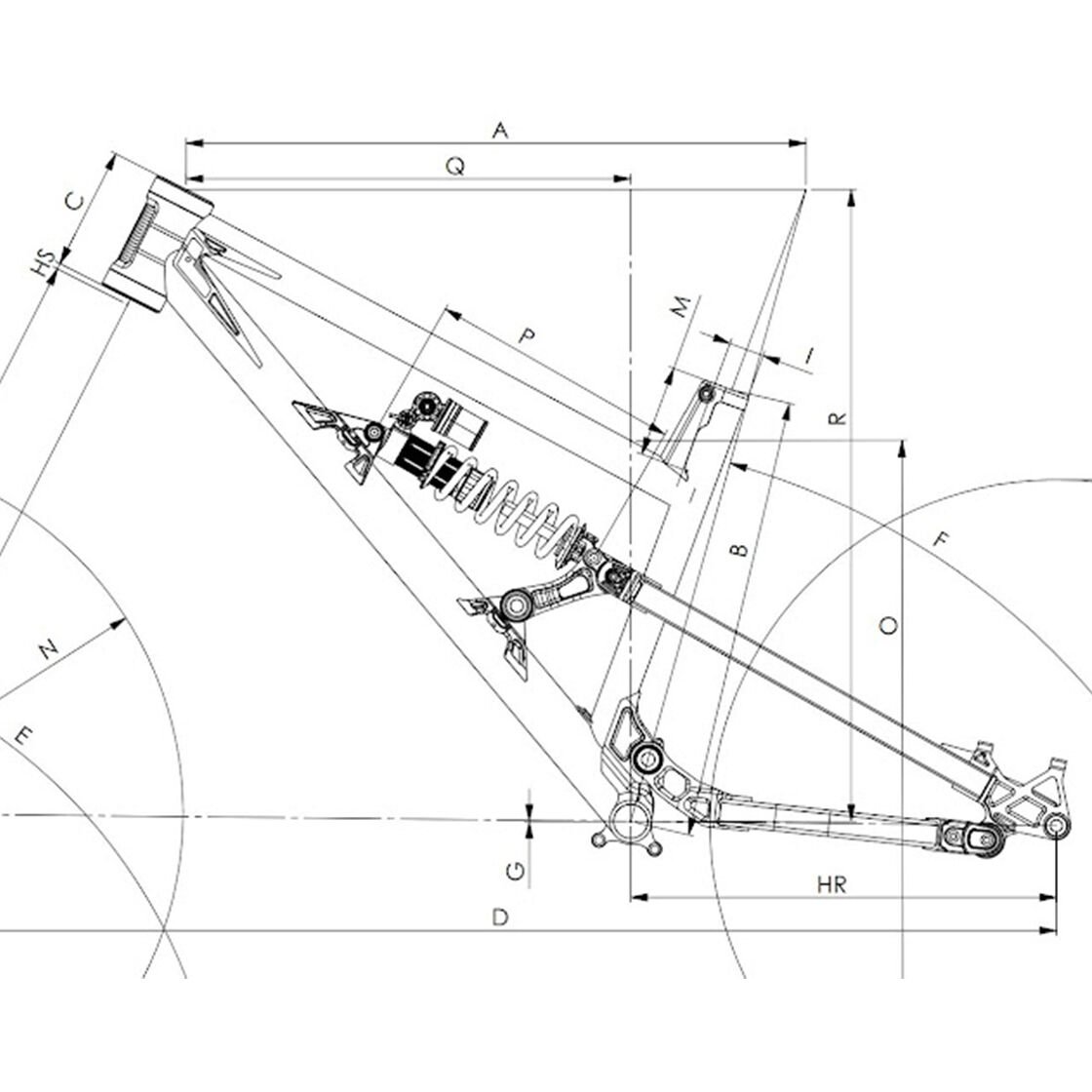
2 frame sizes
Adaptive geometry and load-dependent modification
The G18 Hammer is available in two frame sizes: M and L, as is common with dirt bikes. The dimensions are wider spaced than for other models that we offer in more sizes, which is why we can cover a wide range of body sizes here too. You can find a chart of body and frame sizes in the tech sheets below. Building a perfectly fitting frame means much more than just scaling its basic shape. We take various factors into account here with regard to body proportions and weights. For example adapted tube cross-sections, modified riding angles and particularly low entry and projection heights for S sizes or frame reinforcements that take into account the high weight and greater body strength of XXL frame riders. Saddle position, stem height, length and angle, and handlebar width and height serve to fine-tune the geometry.
7020 aluminum
Sustainable and enduring
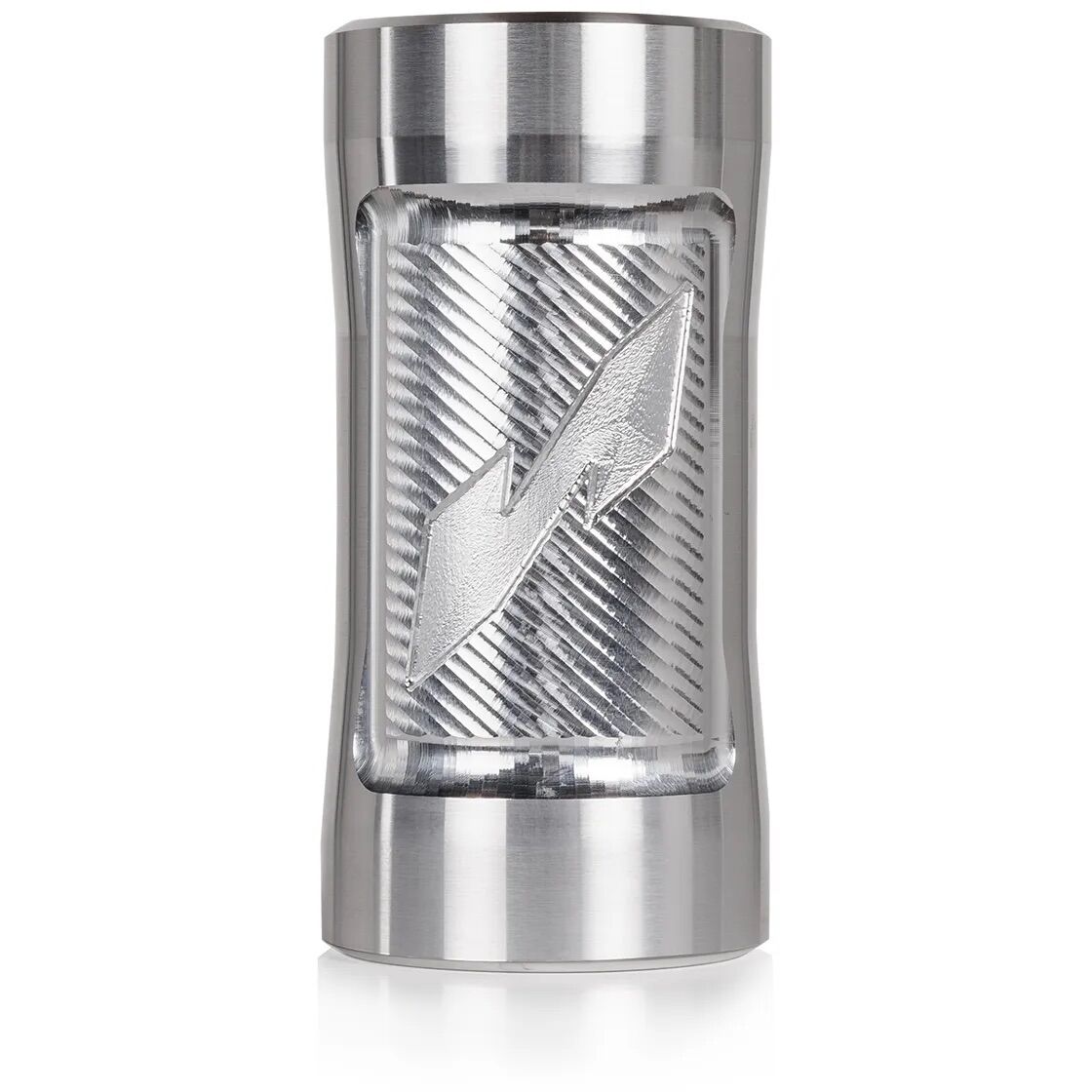

NICOLAI Welding Technology
Craftsmanship and engineering in perfection
We weld our frames by hand using the TIG process. Our welders are specially trained for this and have many years of experience. For each model and frame size, a precise welding fixture is built, called a frame jig. In it, the CNC-cut tube sets are precisely assembled and fixated with all turned and milled parts of a frame that are to be welded. The frame components are first tacked with single spot welds at precisely specified points in a defined sequence and then, to minimize distortion and stresses, welded in several passes. Our characteristic, evenly flat-shingled NICOLAI welds are created by a very slow welding speed. This causes deep fusion of the material and large-area distribution of the loads and forces occurring in the frame.
Extra Love
powder coating and anodizing colors, decals, customizing, individualization
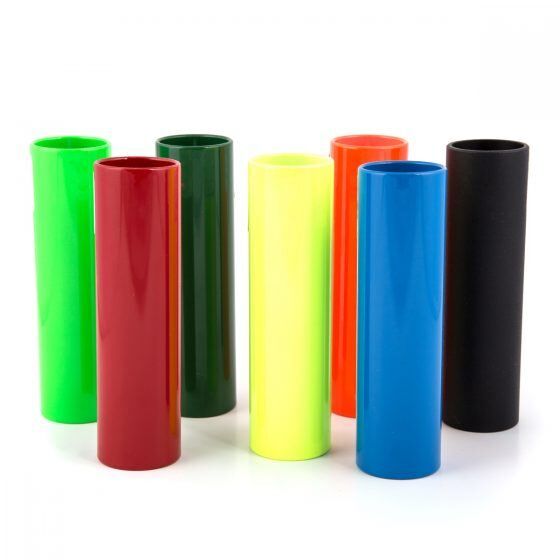
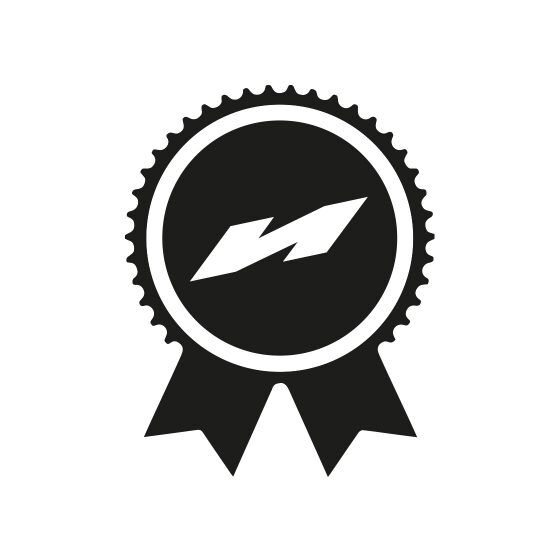
Warranty and spare parts supply
Bike Box
We have developed an elaborate reusable bike box for our mail-order shipping. In it, the new NICOLAI bike arrives protected in a wooden frame and guaranteed safe at the customer and is ready for use after a few simple steps. The same box is reused when the bike is returned to us for repair or service. All shipping protections of the bike box such as pads, lashing straps, brackets and screw connections are also reusable.
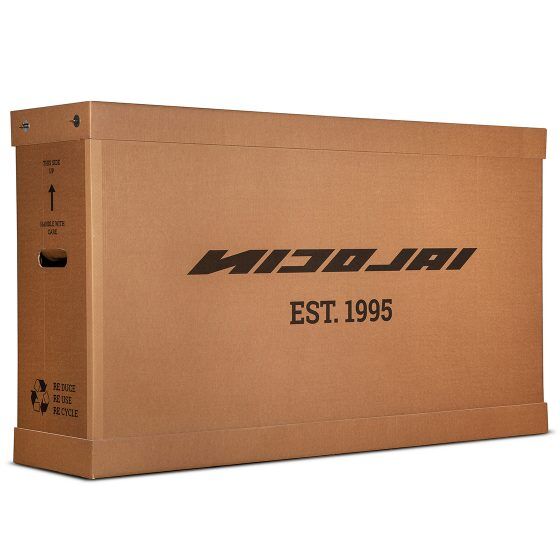
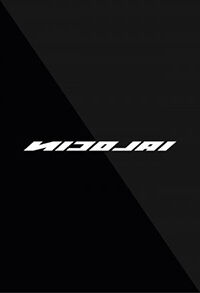
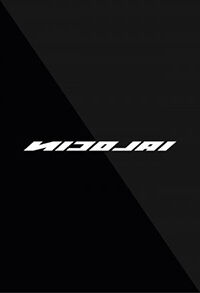